Today, it is not possible to scientifically verify the claims of many factories and facilities regarding water savings, as there is no basic benchmark. But, a study unveiling the water usage in indigo dye process, brings now an universal benchmark allowing to measure sustainability in denim production.
The Transformers Foundation, the denim supply chain platform and think tank for ethics and sustainable innovation in the jeans industry, formed the Indigo Council to study the issue and establish industry standards on February 2024.
The Council includes a coalition of experts from across the denim supply chain, including: Denim mills (Candiani, Crescent Bahuman, Naveena, Diamond Denim, Soorty, Orta, Advance Denim), machinery manufacturers (Morrison Textile Machinery, Karl Mayer), dye and chemistry providers (DyStar), independent technical advisors and auditors (bluesign®).
These stakeholders collected, verified, and analyzed real-world operational data from mills across Pakistan, Türkiye, Italy, and China and prepared the first study. On July 24, 2025 the Transformers Foundation published the report, written by Alden Wicker, award-winning investigative journalist, “A Reference for Water Consumption During Indigo Dyeing”, the first open-source study to define what typical, excessive, and best-in-class water consumption actually looks like in indigo dyeing – across both rope and slasher systems.
There is no one-size-fits-all approach to indigo dyeing
Indigo dyeing is a long and complicated process that involves both chemical and physical reactions, and is influenced by the quality and type of raw materials, production methods, and environmental factors such as weather, humidity, water quality, and more. These factors can vary not only from country to country or region to region but from mill to mill, and even day to day within that same mill.
Moreover, indigo dyeing is deeply rooted in tradition and craftsmanship, with recipes, conditions, and practices varying across cultures and regions. Add in the ever-changing expectations and trends of consumers, and you see that there is no one-size-fits-all approach to indigo dyeing.
The research endeavor was executed through consultation with denim mills globally and overseen by dedicated researchers tasked with data collection and compilation. Both quantitative and qualitative methods are combined to provide a comprehensive understanding of water use in indigo dyeing. By combining data from multiple sources ( interviews, desk research, factory visits) the study provides a nuanced perspective on water consumption in indigo denim dyeing.
This study is only concerned with what happens during the indigo dyeing process and excludes sizing, weaving, and other finishing processes. And, it focuses on two main areas: machinery and indigo chemistry.
For machinery, benchmarks were established for basic fabric construction, shade, depth, and ring effect, with specific machinery types – rope dye and slasher dye – identified for comparison. For indigo chemistry, the study concentrated on liquid indigo applications and aimed to define benchmarks for fabric shades and dye application methods.
With the best practices, water consumption may be decreased to around 3.00 L/kg
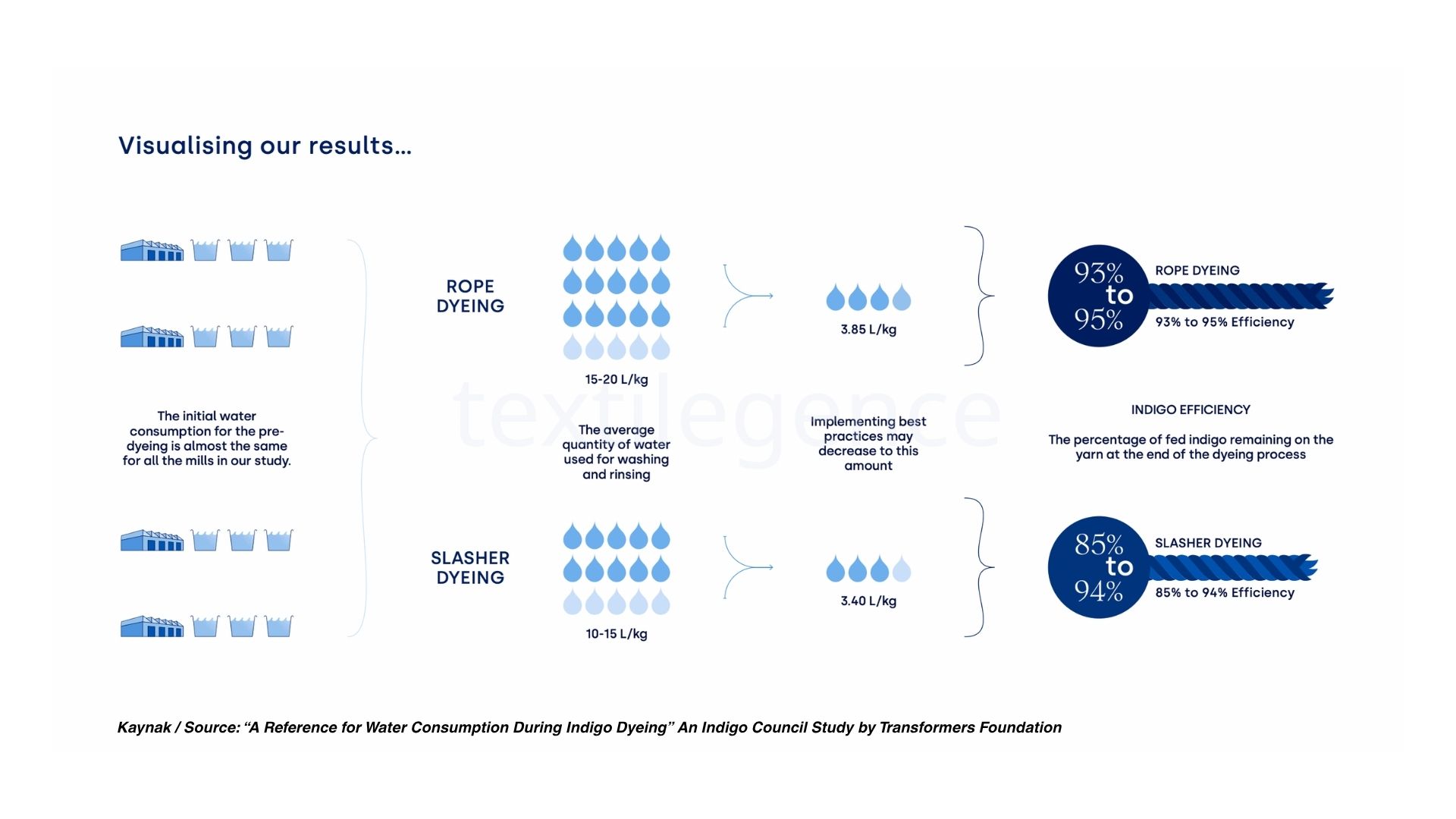
According to the results, the initial water consumption for the pre-dyeing is almost the same for all the mills in the study, the global leaders, known for their high standards of quality and operational efficiency. The average quantity of water used for washing and rinsing is 15-20 L/kg in rope dyeing and 10-15 L/kg in slasher dyeing. The study shows that implementing best practices may decrease these numbers respectively to 3.85 L/kg and 3.40 L/kg.
The calculations, based on the data collected from denim fabric mills, depending on all the constants and variables including in the chart, shows that total water consumption in the washing boxes after dyeing are vary between 3.40 L/kg and 15.00 L/kg.
The percentage of fed indigo remaining on the yarn at the end of the dyeing-washing process rate of up to 97% achieved when using low amounts of water is remarkable.
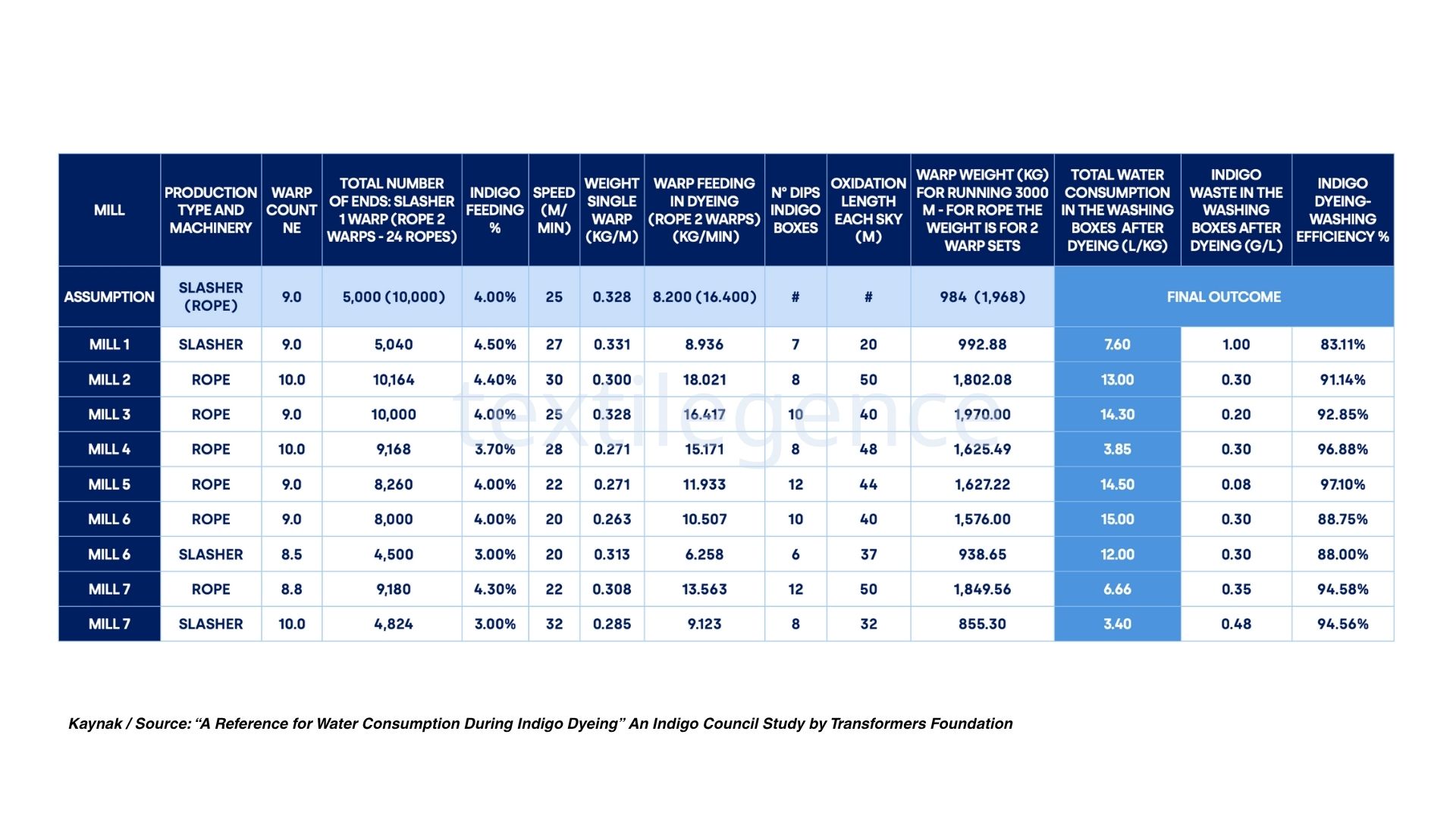
The report represents a significant milestone, by demonstrating that reducing water consumption in the standard indigo dyeing process for warp yarn is achievable, providing that the challenge is approached with a scientific and data-driven mindset.
The Indigo Council is currently exploring future benchmarks around wastewater treatment, indigo recycling, finishing, and lower-impact dyeing technologies as well.