The sustainability achievements of five important Monforts denim customers in Turkey were featured in Lenzing’s Carved in Blue. Denim mills around the world make innovations for UN Sustainable Development Goal 13 on climate action. Article titled ‘SDG 13 Steps: How Turkish Denim Mills are Embracing Climate Action’; details how Bossa, Çalık Denim, DNM Denim, Kipaş and Orta Anadolu (Orta) reduce their carbon footprints.
Bossa, one of Monforts denim customers, prioritizes energy efficiency
Bossa, having not yet set official carbon footprint targets, continues their efforts to reduce carbon emissions. The denim manufacturer taking steps on energy efficiency using the ISO 5001 Energy Management System as a guide for their policies and provides 50% of the company’s energy needs within their own plant which has more than 18,000 solar panels on its roof and a co-generation (combined heat and power) system to reduce the reliance on outside energy. In addition, Bossa reduces its environmental impact by recycling their post-industrial wastes into new materials, with the goal of reaching 15 percent recycled fibre input by 2021.
Çalık Denim switched to using natural gas instead of coal in steam production
Çalık Denim’s Transformation Lab works to lead progress in SDGs (Sustainable Development Goals) through industry collaborations such as the Ellen MacArthur Foundation’s Jeans Redesign program. Çalık Marketing Communication Executive Selen Ergül stated that while global warming affects the life of humanity, they continue to work to reduce carbon emissions in their activities within the scope of UN SDG 13 – Climate Action. In this regard, she explained the 2025 sustainability targets that directly affect carbon emission reduction as follows:
“Reducing carbon emissions per unit production by 20 percent compared to the year 2018; increasing renewable energy generation by 10 percent compared to the year 2020; and increasing electricity purchases from renewable sources to 50 percent. One of the most valuable steps we have taken in this matter is we have quit coal in steam production from July 2021. We now use natural gas for steam generation. Thus, we will gradually reduce our carbon emissions from fossil fuels”.
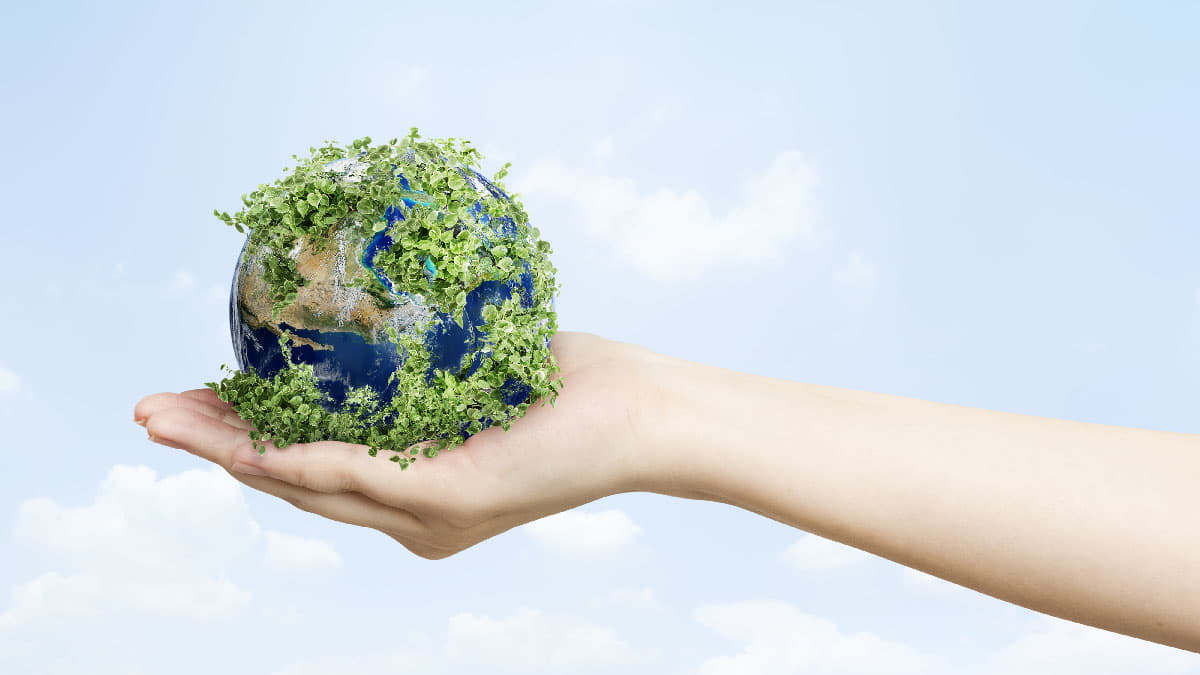
DNM Denim saves energy with their waste management strategy
DNM Denim reduced its carbon impact by 10 percent in 2020 compared to the previous year and supports the development of low-emission products and integrates their energy efficiency strategy with a low carbon strategy for this purpose. DNM Marketing Executive Zuhal Karaçayır stated that the carbon footprint calculation work comprises verification in line with the EN ISO 14064-1:2012 and made the following statement regarding the other activities carried out by DNM Denim within the scope of SDG 13:
“DNM Denim has a waste management strategy that includes an incineration plant. This system operates at 1400 degrees Celsius, deactivating all hazardous waste while saving 15 percent natural gas for steam generation, which is then reused during the wet process. To reduce greenhouse gas emissions, these operations are carried out with sophisticated filtration systems. As a result, we were able to eliminate chemical waste and save energy”.
Kipaş aims to be a ‘climate positive producer’ by 2030
Kipaş is on its way to becoming a ‘climate positive producer’ by 2030 investing in machines powered by natural gas and solar panels that provide 12.3 million kWh of energy annually. The manufacturer is also targeting carbon emissions from their wastewater by using the carbon dioxide from their coal boiler to neutralize the sodium hydroxide (NaOH) in the wastewater. Kipaş increased the production output from 57 million metres of fabric to 72 million metres between 2018 and 2020, while the mill’s greenhouse gas emissions decreased from approximately 215 million kg to 111 kg.
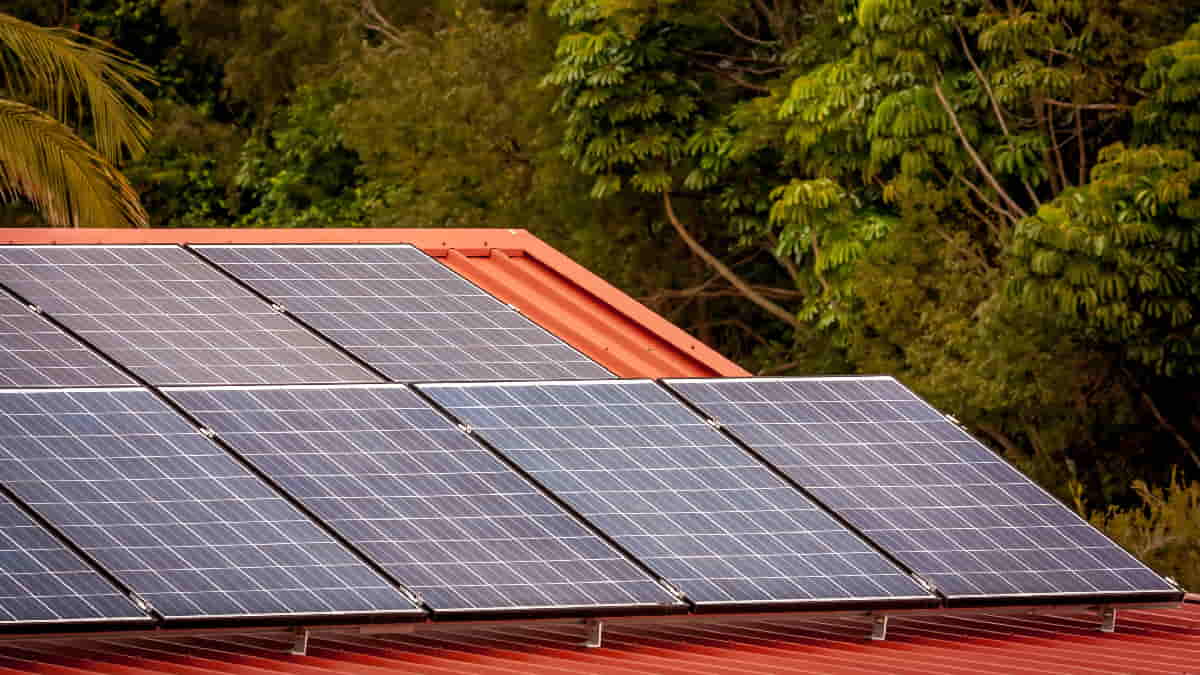
Orta uses 100% renewable energy in their spinning and weaving facilities
Orta started to use 100% renewable energy in their spinning and weaving facilities in 2020, and today they generated 96% of the purchased electricity from renewable energy sources. They also assess every newly-developed fabric’s potential environmental impact via LCA and shares the data through QR codes on product hangtags.
Orta Sustainability Specialist Sebla Önder announced that they started using 100% renewable energy in their spinning and weaving facilities thanks to the initiatives they started in 2020. Önder stated that 96 percent of the purchased electricity today is generated from renewable energy sources which accounts for 40 percent of their total electricity consumption, and said; “This saves around 15,000 tons of CO2 emissions annually, which is equivalent to carbon emissions captured by 45,000 trees”.