To accelerate their weaving and finishing processes, Arthanari Loom Centre Textile Pvt Ltd (ALC) decided to invest in its own ring spinning and winding unit. Instead of buying 12 tons of yarn per day, ALC will integrate the yarn production into their facilities with ring spinning machines and ten Rieter Autoconer X6 with Preci FX, a software-controlled yarn traversing system.
When yarns are purchased as hard packages, they must be rewound before and after dyeing. For dyeing, cylindrical packages with lower density and cropped edges are required. After dyeing, the packages are rewound into conical shapes to enable efficient unwinding during warping and weaving. These additional process steps increased labor and production costs. Preci FX eliminates the need for rewinding and cropping before dyeing. A. Alagarasan, Managing Director of ALC, explains the transformation of the production process: “The investment in our own spinning unit enables us to drastically shorten our process chain.”
Reduced rewinding steps and lower production costs
The use of Preci FX allows ALC to produce dye packages with a weight of 1.7 kg instead of 1.65 kg, which leads to better machine utilization and savings in water, dyestuff, and energy per dyeing process. Thanks to the drumless winding technology, dye packages with rounded edges are produced. The dyed packages can be directly used in the warping and weaving process.
Minimized yarn waste and high package consistency
With the high-precision length measurement system Ecopack FX, package weight variation is minimized. This reduces yarn waste during warping and increases process reliability. ALC reports a cost saving of INR 5 per kilogram and process step. With a daily output of 12 tons, this results in annual savings of INR 21.72 million. The ten machines are operated with only three operators.
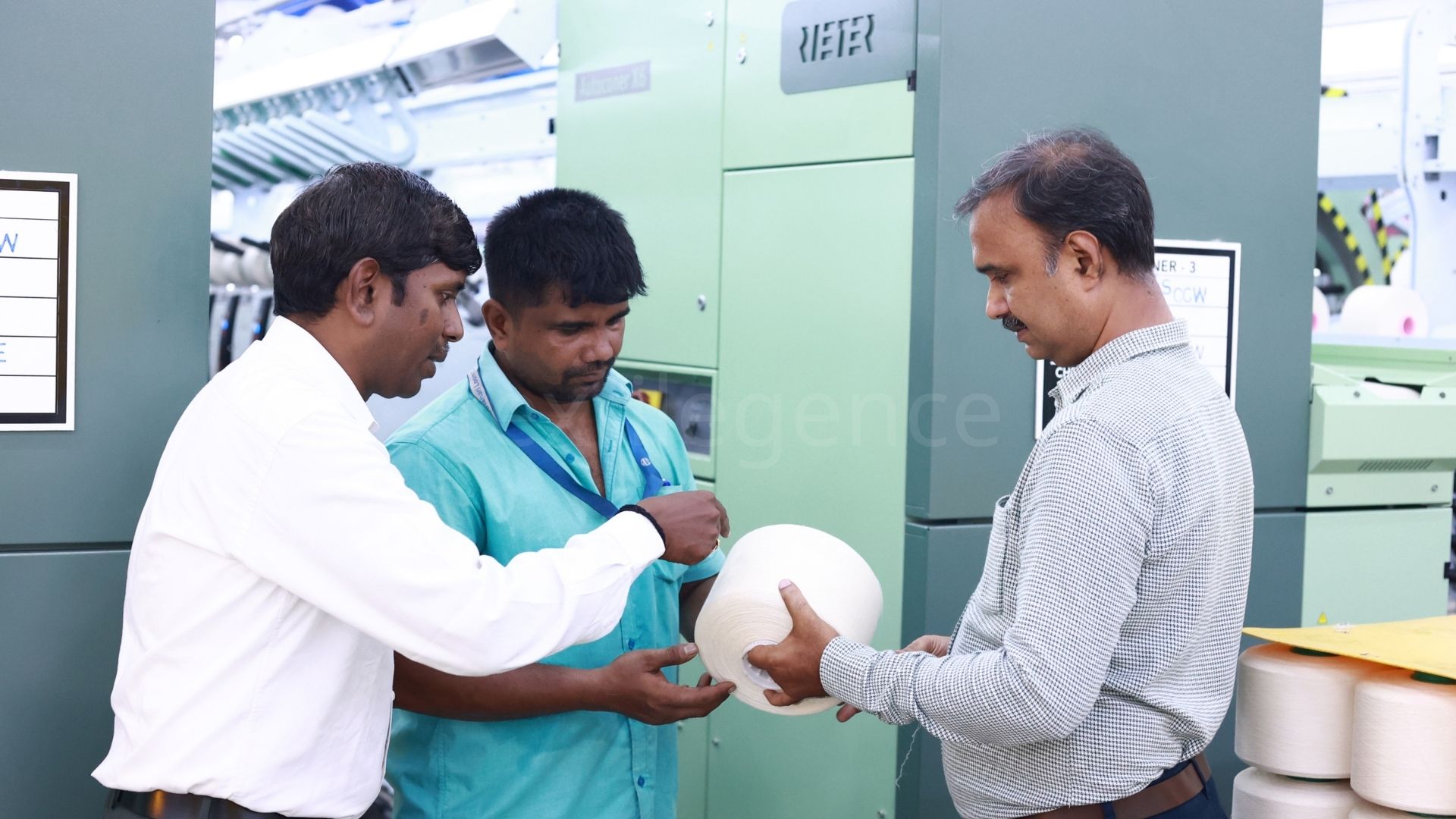
Alagarasan highlights the advantages: “With Rieter’s support, we benefit from lower operating costs, lower energy and water costs and lower labor costs. We can operate the ten winding machines Autoconer X6, type V with only three operators.”
Exceeding expectations
The addition of the winding unit has shortened the process chain, making it more efficient – delivering more than promised. Alagarasan looks ahead with confidence: “This investment in the spinning process marks a new chapter in our company’s ability to remain competitive and deliver world-class products to our customers in India and abroad with greater speed and flexibility. Our expectations have been exceeded.”