Technology pioneer Mitsubishi Electric performed the European launch of the “Industrial Internet of Industrial Sewing Machines” application at the International Textile Equipment and Technologies Fair Texprocess 2017; held in Frankfurt on May 9-12, and explained its advantages. Visitors have had the opportunity to see the productivity and quality enhancements of Mitsubishi Electric industrial sewing machines and automation solutions in the context of Industry 4.0 which were provided through the Industrial Internet of Things (IIoT) connection.
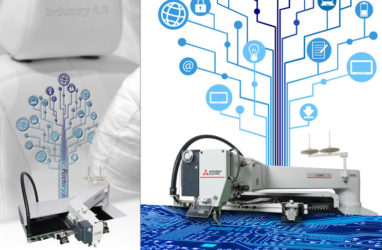
The new industrial sewing machines used in many different sectors, especially in the textile and automotive sectors, are becoming more and more intelligent. At this point, the pioneer of technology, Mitsubishi Electric, is highlighted by its industrial sewing machines enriched with automation technology that offers enhanced intelligence. Mitsubishi Electric welcomed its visitors at Texprocess 2017, Frankfurt, Germany, from May 9th to 12th. And has presented the European launch of the “Industrial Internet of Industrial Sewing Machines” application; which responds to current industrial requirements. Noting that industrial sewing machines are no longer purely stand-alone devices in today’s market conditions; where competition is high and high value added products are preferred; Mitsubishi Electric explained how industrial sewing machines and automation solutions compatible with Industry 4.0 boost the productivity and quality through Industrial Internet of Things (IIOT) and how it can help reduce maintenance costs.
Live demo with six Mitsubishi industrial sewing machines
In Texprocess 2017, a live demo was performed with six Mitsubishi Electric industrial sewing machines; connected to a higher level control system. The actual process data was transferred to the HMI; a touch screen of the Mitsubishi Electric GOT2000 series; which is located on each of the sewing machines and displays MELSEC PLC data. This practice allows manufacturers to see if quality standards are being met. Whether there is any other action that needs to be applied to increase quality. Visitors have also been able to see how the data of industrial sewing machines exhibited at the fair; data is put together with the help of Mitsubishi Electric’s MAPS SCADA software.
Industrial internet of Mitsubishi sewing machines
With Mitsubishi Electric’s “Industrial Internet of Industrial Sewing Machines” application, manufacturers can see the working time of each machine; determine which workstations are more efficient than others and why. Thanks to the production data collected in the system, manufacturers can take appropriate steps to increase performance or machine suitability; based on real information instead of assumptions. In addition, the information provided by these intelligent machines makes it possible to plan service and maintenance activities if requested. Such a way of working instead of predetermined maintenance programs has a positive impact on productivity and profitability; by helping to increase the working hours of the machines and to reduce costs.
“Quality Assurance” instead of “Quality Control”
The high productivity that Mitsubishi Electric provides in industrial sewing machines also brings consistent high quality in production processes. The new generation of sewing machines can easily be integrated into a wider range of quality assurance processes; such as systems that remove selection errors. These faults can occur, for example; when picking up pieces of material for the frame to be sewed; by taking the wrong part or by using the wrong sewing frame to load the machine.
With the Poka-Yoke (Error Prevention) System, Mitsubishi Electric, which aims to contribute to reducing the margin of error, allows operators to select the right material parts for frame loading on the sewing machine. The barcodes on the sewing frame are scanned by the controller to ensure that the correct frame is used to load the machine for a specific sewing operation.In addition, the machine control system, as an additional quality assurance measure before the start of sewing, controls the material thickness according to predetermined parameters. As another quality control method, manufacturers can capture images of finished products with special cameras and compare the quality of the sewing with the stored high resolution image.
Thanks to all these features and functions found in Mitsubishi Electric’s Industry 4.0-compatible next-generation industrial sewing machines, textile manufacturers can switch from quality control to quality assurance. It will also be possible to store the complete production information to enable traceability in the entire supply chain.