One of Turkey’s leading knitted fabric printing and dyeing company, Sezginler Tekstil has achieved significant benefits by investing in Baldwin Technology‘s innovative non-contact spray system Texcoat G4 for finishing process. Having a production capacity of 56 tons per day, the company added 4 TexCoat G4s to its stenter lines in order to solve the finishing quality issues and time consuming dilution occurrences, especially in the wet-on-wet softener process. The company achieved increased uptime, exceptionally even finishing quality, and considerably reduced chemistry and energy consumption. In addition to practically zero chemical discharge, Sezginler Tekstil reached the capacity of single-sided finishing in fabric with its uninterrupted smooth finishing quality.
The finishing application system, TexCoat G4, was introduced to Sezginler Tekstil by the Turkish textile machine vendor, Spot Tekstil, a highly regarded partner of Baldwin. Since the first machine purchase, the company has achieved many benefits in the application of finishing chemicals with non-contact spray technology. For this reason, it acquired a total of 4 TexCoat G4 machines with its subsequent investments and expanded its finishing capacity in this area.
Texcoat G4 put an end to the finishing quality problems of Sezginler Tekstil
At the time, the company utilized the conventional pad/foulard method, and experienced quality issues and time consuming dilution occurrences, especially in the wet-on-wet softener process. Sezginler Tekstil has integrated TexCoat G4 into the production stage to overcome this problem. Finishing could now be done wet-on-wet via pad/foulard followed by the non-contact spray system. Sezginler Tekstil now uses the four non-contact spray systems in both wet-on-wet and wet-on-dry processes and experiences high uptime, consistent quality and practically zero chemical discharge.
Sezginler Textile Finishing Manager Ali Küçükerenköy said that by using the TexCoat G4 in the wet-on-wet process with reactive dyed fabric, they get a uniformity of the fabric that they have never experienced before. Küçükerenköy said; “Adding the non-contact spray technology to the pad/foulard, is a decision we will never regret”.
One of the major challenges of using pad/ foulard is that the chemical concentration changes continuously during production and needs to be adjusted every 1000- 1500 meters, depending on the type of application. This is not the case with non-contact spray finishing.
Saving time and chemistry
Mehmet Ali Küçükerenköy said; “With TexCoat G4, we can totally rely on a continuous and even application from the first meter of the fabric to the last”; and continued his words saying; “The same amount of chemical concentration is applied throughout the production; which was never the case with the old finishing method; where every meter of the fabric could have variations as the pad/foulard also being dirtier each meter”.
In addition to the mentioned issues of the pad/foulard, it frequently needs to be drained of chemistry; as much as 50 litres, depending on the production. This equates to a considerably amount of chemistry and time going to waste at every drain. However, all the above issues are completely eliminated for Sezginler Tekstil with the four TexCoat G4 systems running.
Küçükerenköy said; “We don’t need to spend time on pad draining anymore and can anyway rely on a consistently even chemical concentration. It is clear that the TexCoat G4 has given us great production advantages; in regards of saving considerably amount of time and chemistry”.
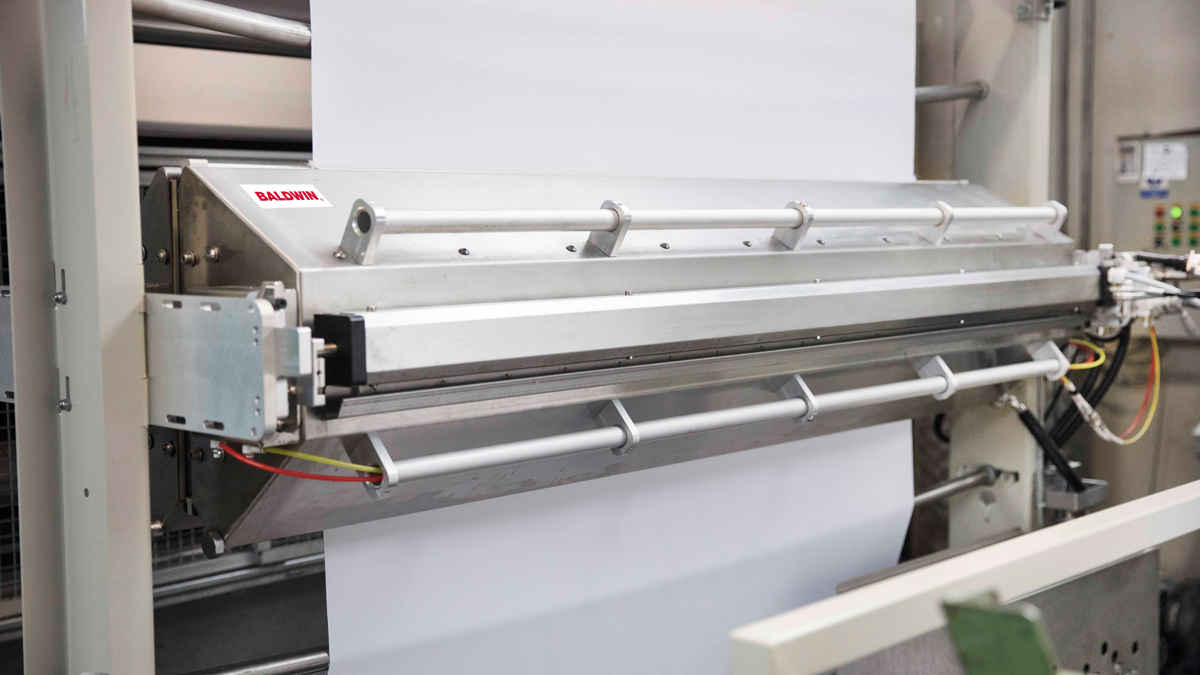
50% less energy consumption with TexCoat G4
Sezginler Tekstil’s energy consumption for drying reduced as much as 50% in the wet-on-dry application, thanks to the TexCoat G4. The non-contact spray system allows for a higher concentration of chemistry mix with lower pick-up requirements. And with less wet pick-up; the fabric can pass through the stenter faster and with lower heat, reducing the energy consumption.
Another advantage of the TexCoat G4 is the option of applying chemistry to one side of the fabric. This is of high value when running printed fabric –which Sezginler Tekstil regularly does; for avoiding unwanted pigmentation on the prints or when running fabric with one-sided finishing characteristics. Applying chemistry on just one side is very cost-efficient; since the chemistry consumption will be 50% less compared to a dual-sided application.
In a true success story; Sezginler Tekstil installed the TexCoat G4 spray finishing systems and gained increased uptime; even finishing quality, and considerably reduced chemistry and energy consumption.